Here is the build along that I promised earlier for a fiberglass mesh and epoxy takedown. I got the
idea from RyanO and he got it from another bowyer. It really works like a charm. The first thing you
need is a bow to practice on. I would not do it to my favorite bow the first time, just incase something
goes bad. For this one I am using a hickory backed pecan bow that I got in trade many months ago.
You are going to need the following:
2 ton epoxy
Fiberglass mesh ( auto body)
plastic wrap
masking tape
2 wood or sheet rock screws
small drill bit with drill
the sacraficial bow
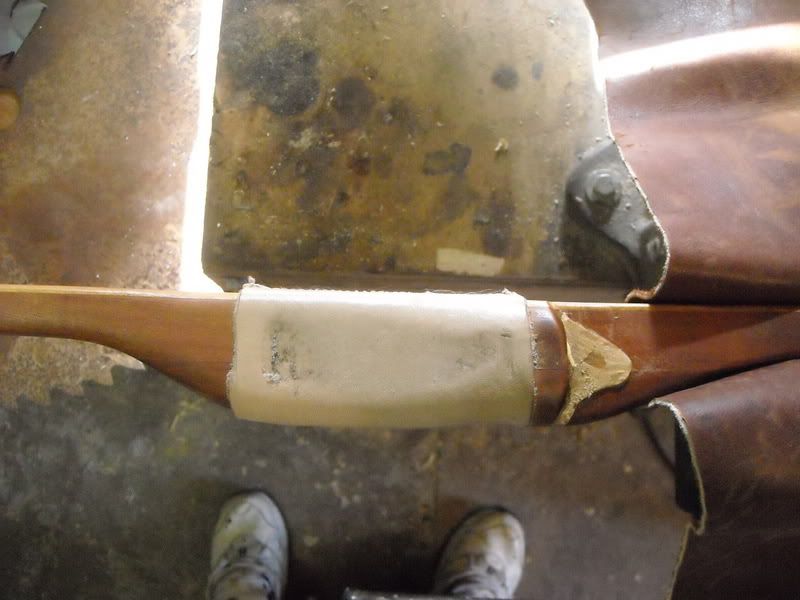
Take the handle wrap off and save it if you want to for another bow, because it will not fit this one anymore.
Once it is gone, cover the upper limb with leather to protect it and lock it in a vise, but not too tight, then
mark out a four inch handle, wherever you want the take down to be. Now make a diagonal line from the
lower line at the back of the bow to upper line on the handle side.
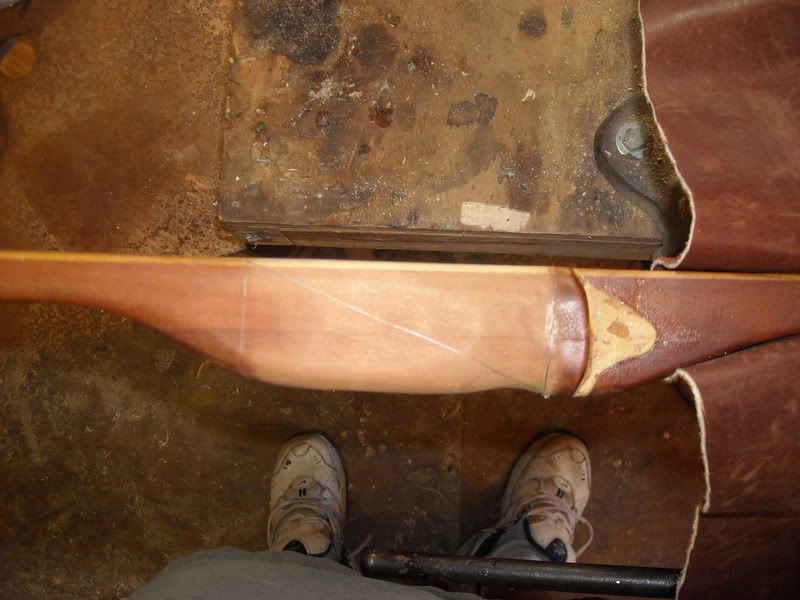
Now flip the bow in the vise so the handle in facing up. Measure down 1 inch from the top line and mark the
spot to be bored. I know someone just said, "Do what? Bore?" The hole needs to be a little smaller than the
wood screws you are going to use to hold the bow together temporarily. Yep, there is a good reason for this.
Using a small bit drill a hole straight into the handle, then counter sink it. Later on, the countersink will fill with glass
and epoxy and form a nipple which will help lock the lower limb into the upper limb.
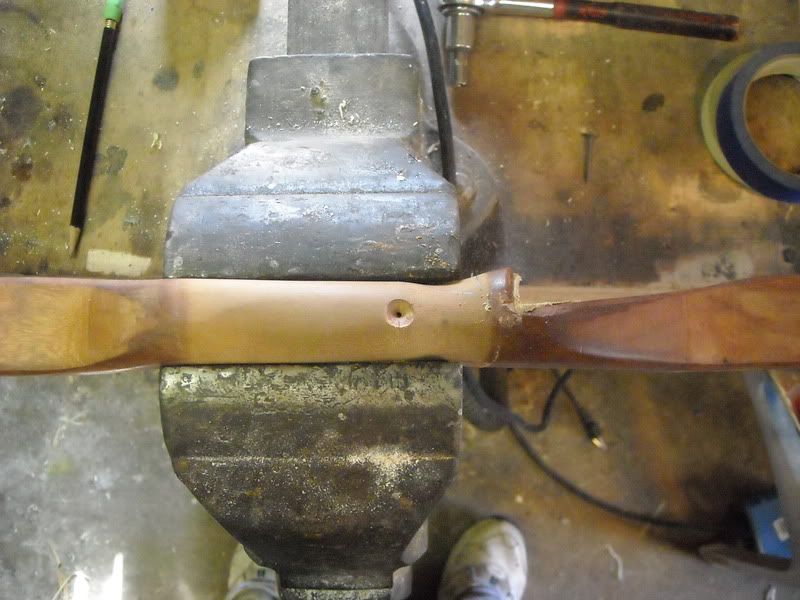
Now flip it so that the back of the bow is facing up in the vise and bore a small hole 1 in from the bottom line.
Do not bore all the way through the bow.
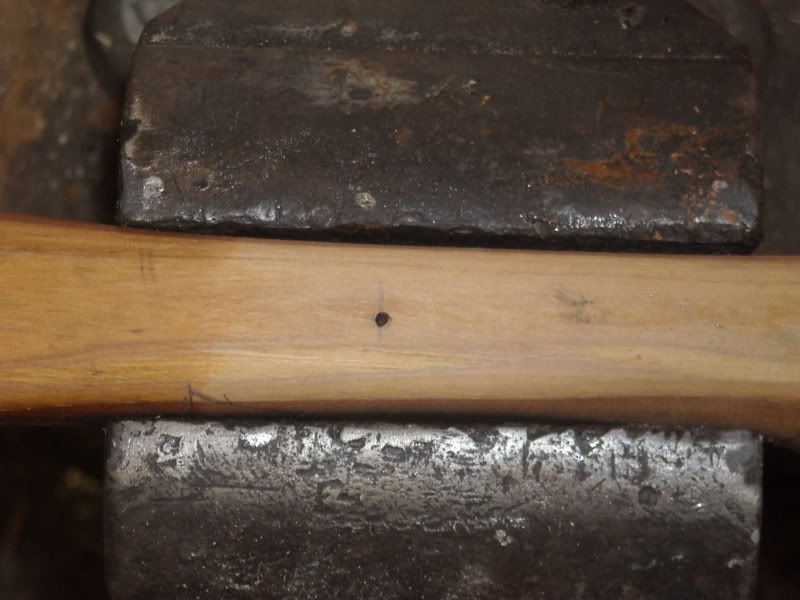
Now for the scary part. Cut the bow in two on a bandsaw ( Somebody just Cringed) being careful to stay on the
line as much as possible. You got one chance, so don't mess up.
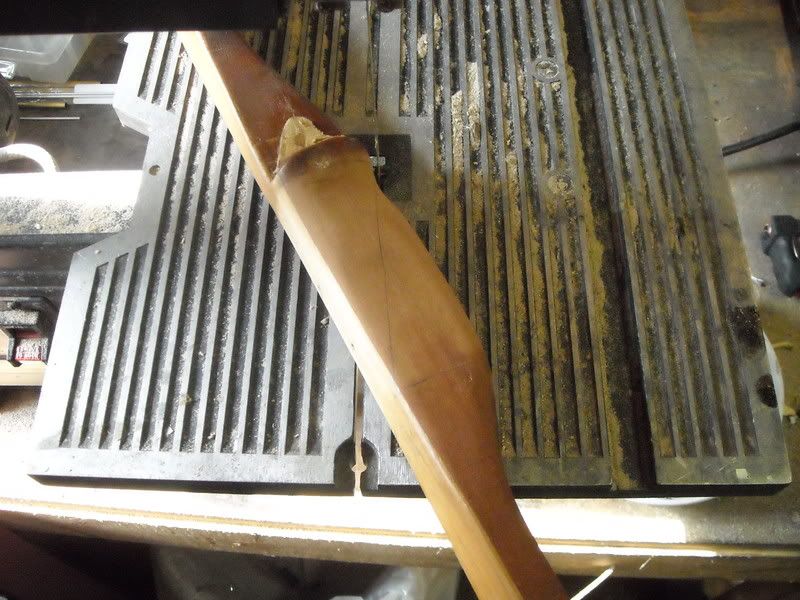
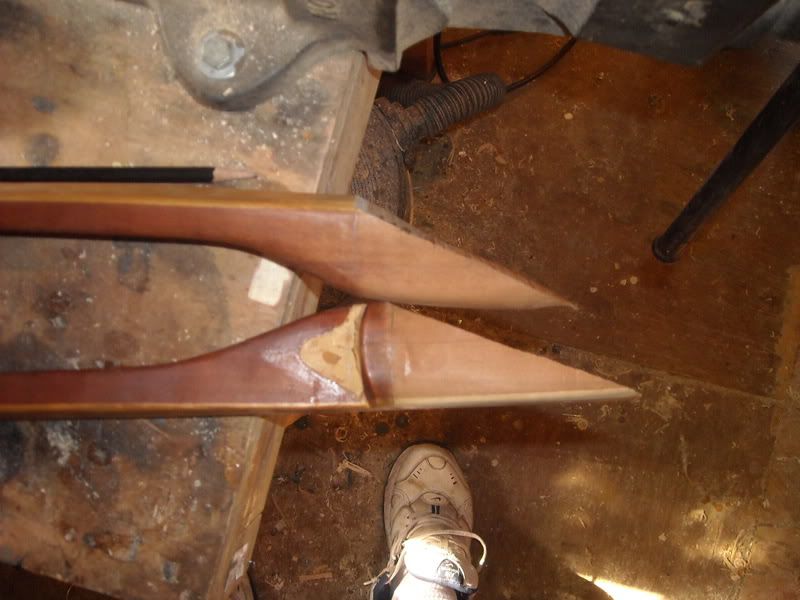
Now go grab some plastic wrap from the kitchen and some masking tape. Put a few rounds of tape just above the
top line and just below the bottom line, then rip off a foot or so of plastic and tape it to the upper limb where you put
the tape earlier. Then do the same for the lower limb. This will keep the epoxy from getting all over the bow limbs.
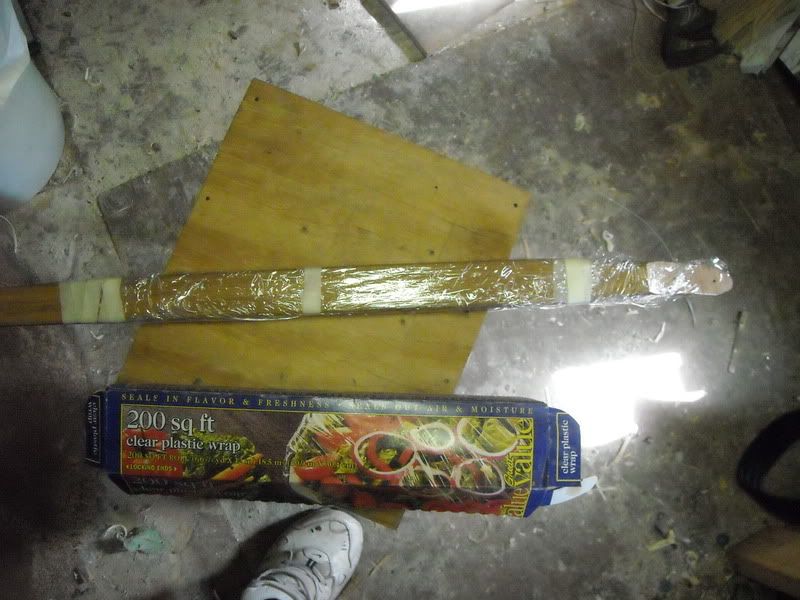
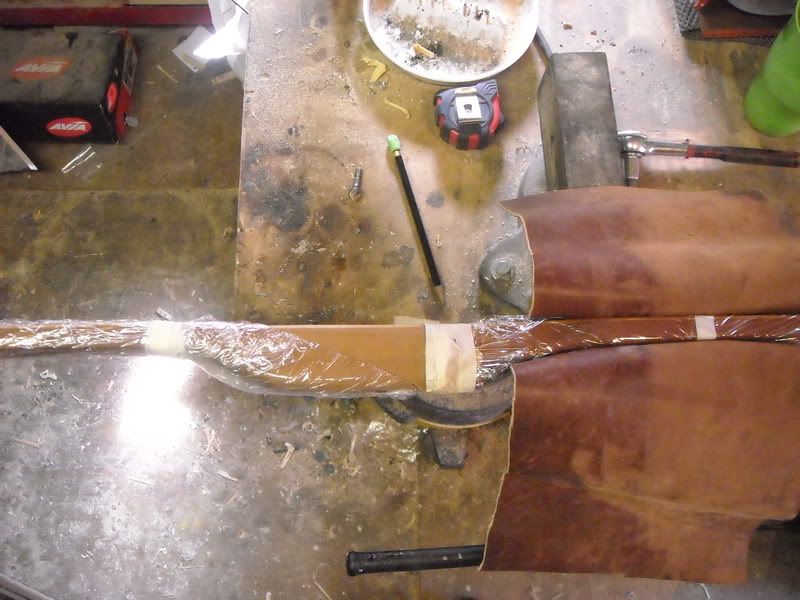
Check the alignment with some string to make sure the limbs are aligned. Insert the screws tight enough to hold
the bow together, but not tight enough to crack it. Now you need the fiberglass mesh used for auto body repair
and some 2 ton epoxy. I forgot to take a pic of the alignment, but I am sure you can figure that part out. Before
applying the epoxy, give the plastic on the lower limb ( covered in plastic) a good coat of mink oil,
crisco or anything really greasy where the handle will be. You do not want the bottom limb to stick to the epoxy, just the top.If the bottom
limb gets adhered to the inside of the handle, you will have to grind it all off and start over.
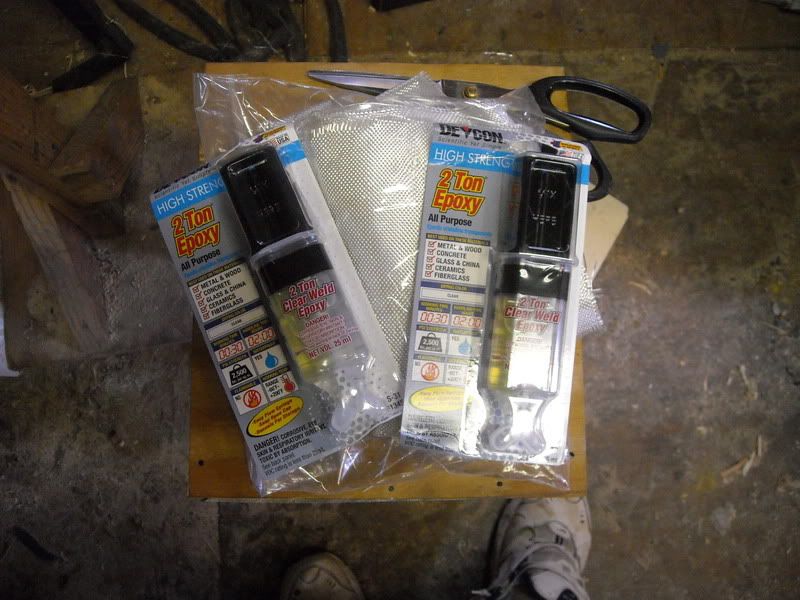
Now squirt out about half the tube of epoxy on some thick paper like this file folder and mix really good.
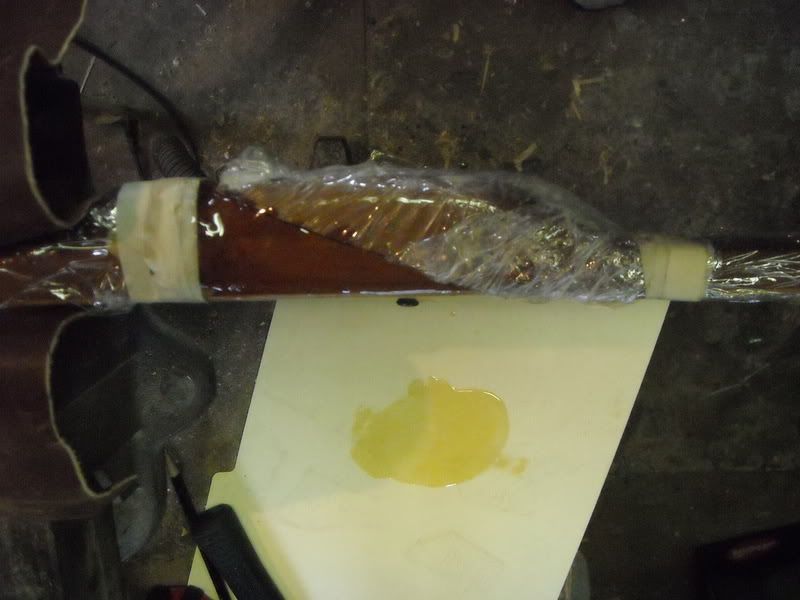
Now cut a few two inch wide strips of the mesh and fold them lengthwise. OK, the messy part. Put on latex gloves
and get a mess of the epoxy on your hand and smear it around where the new handle will be. Now grab one strip of
mesh and wrap around the handle, keeping the fold to the outside of the handle. This will help keep the raveling mesh
to the inside of the handle. Wrap in a spiral until it runs out, being careful to stay away from the screw heads. They
will be removed later. Grab another strip and keep wrapping until the handle is pretty much covered except for the screws.
Use the rest of the epoxy to coat the outside of the mesh, giving it a little twist once in a while to keep the wraps tight.
After 3 strips about 18 inches long, it will look something like this. A mess.
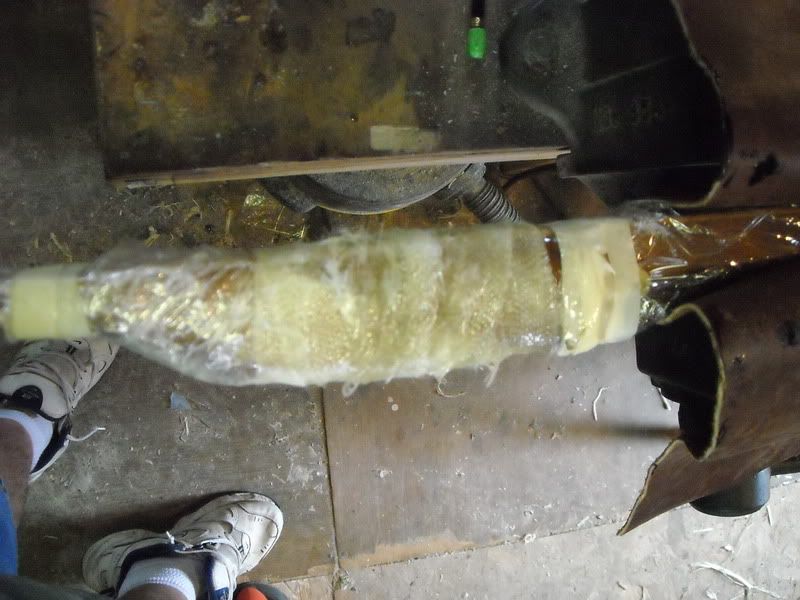
Now set it up to dry. It will be cleaned up and finished tomorrow. Most of the mess can be cut or sanded off before the
final layers are added. For a 55 to 60# bow it will need to be about 1/8" thick. Lighter weight bows around 35# can be
about 1/16".