Very welcome.
Now we come to the really unpleasant task of binding in the prod. I imagine the apprentice had to do this back in the 14th century. You will use every black word you know, make up new ones, and Google foreign cuss words as you work through this process.

The secret is thread management, and man alive, these threads will come alive and want to explore every inch of your workshop, get wrapped up in themselves, the drill press, the vices, the bench legs, your legs, your knees, the lighting fixtures, and the neighbor’s cat. Don’t let this happen! Fight them. Be stern, and if you have to, toss them in the trash and start over.
But from the beginning. I started with a new roll of 8/6 linen thread, which is nice and thick, heavy stuff that looks very medieval. This is undyed and unbleached and has that nice natural look to it. It doesn’t stretch much, and is not too expensive (maybe 25 bucks for a roll). I get it from a supplier to weavers and knitters near me, but you can probably find it on line. You can also use hemp, which was used historically, and probably 1/8” stuff is ideal.
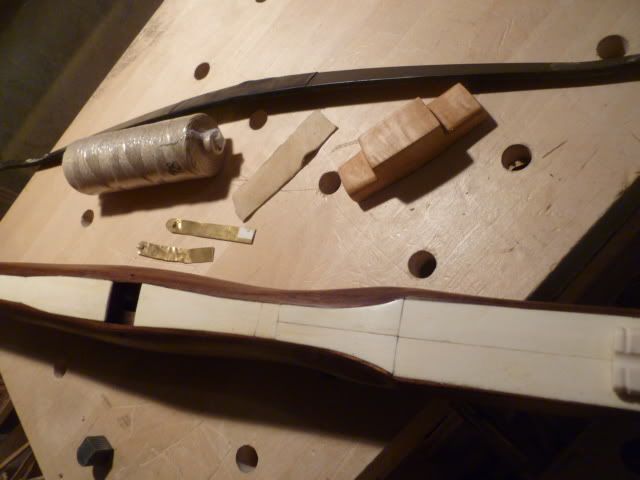

You measure out a long, long, long single thread. I used my eye and estimated about 50 yards, or 150 feet. Way better to have too much than to realize you don’t have enough when doing the final binding. So, I started by slipping the thread through the binding hole. So far so good. The prod is padded with a couple of pieces of buckskin, on that went between the back of the prod socket and the prod, and the other between the front (back) of the tiller and the tiller binding block. Note that the finish on the tiller binding block is not perfect, and I figured that, one, having a bit of bite or tooth will be good to help lock in the binding, and two, it will never see the light of day

.
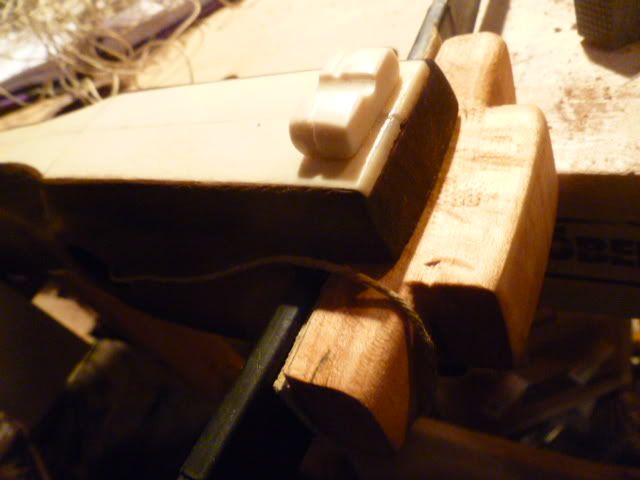
So, slip one end of the thread through the binding hole, being careful not to tangle it or tangle it with the other end of the thread. It will want to do that, and likely will. If you look at it just right, it will tangle. And it will end up in Hoboken, all tangled up and hanging out in a sleazy bar.
Thread management is the key. After giving up doing this in my shop, I moved to the kitchen, cleared the decks, and worked there. Yes, everything was hopelessly tangled, and I tossed out not one but two attempts, so there was about 300 feet of linen thread ruined and laughing at me, and this was about 4 hours into the process.

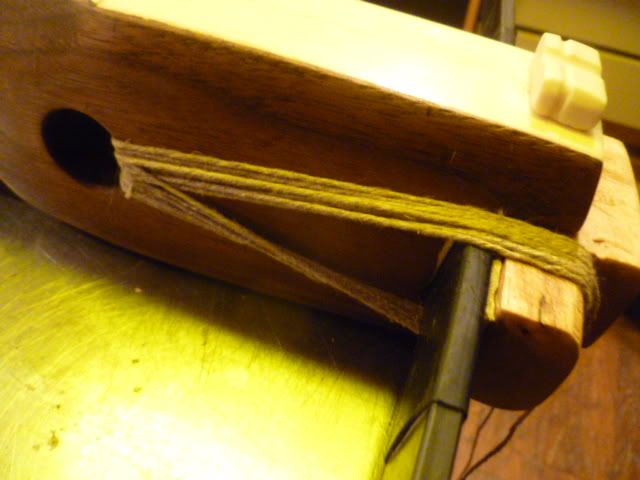


Finally, with the third go, things went well. I can’t say how many revolutions I went through to get the prod where I felt it was nice and tightly bound in, but common sense and a bit of prodding and pushing will tell you when you are done. I am guessing I used up about 3 fifths of the 50 yards, and certainly more than half.
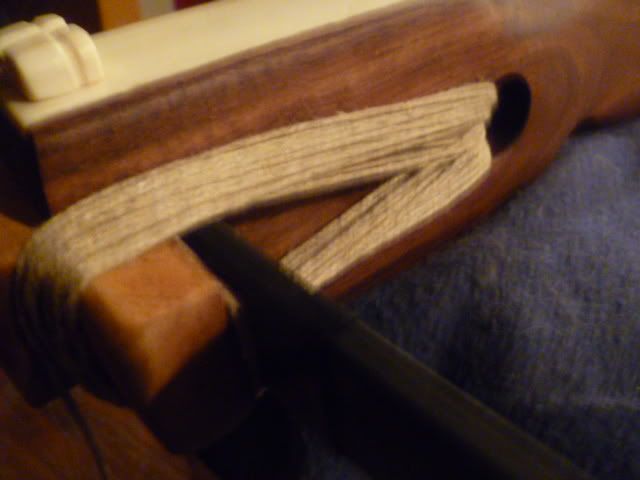

Now, you will find the prod is still not rock steady in the socket. Time to do the side bindings.
I probably should put up some sketches, but basically, you take the two ends of the threads, place the crossbow on its side, and begin this part. I began at the prod or business end of the weapon, but you can begin the side bindings at the hole end, too. A discussion about binding methods on a crossbow forum (arbalest guild) taught me a new method, in that I began binding the figure eight part of the binding at the pod end and then move aft, toward the prod binding hole (i.e. the butt end of the weapon). It would be prefectly acceptible to start at the binding hole and move toward the prod. I think this gives you a tighter overall binding, however.
This is done using a figure 8 pattern: under, through, over, under, though, over, etc. I did this for 13 full revolutions or turns, keeping the thread as tight as I could without breaking it to bring the two sides of the skein together. Depending on many factors with your own crossbow, such as the diamter of the binding hole, length between socket and hole, type of thread and diamter of thread, etc, you may find 20 revolutions are needed, or 8. Each time will be unique.


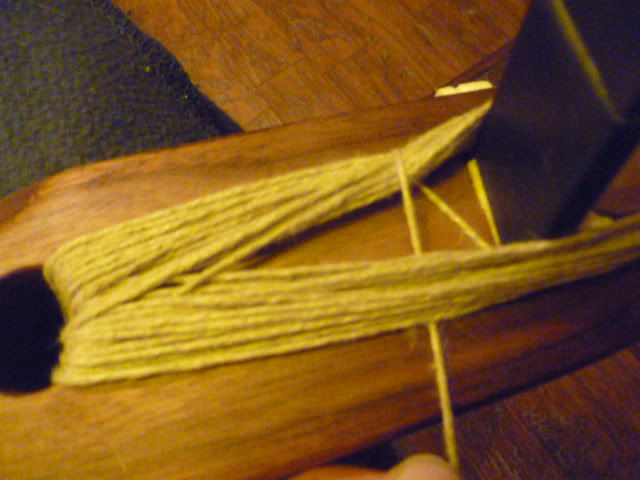
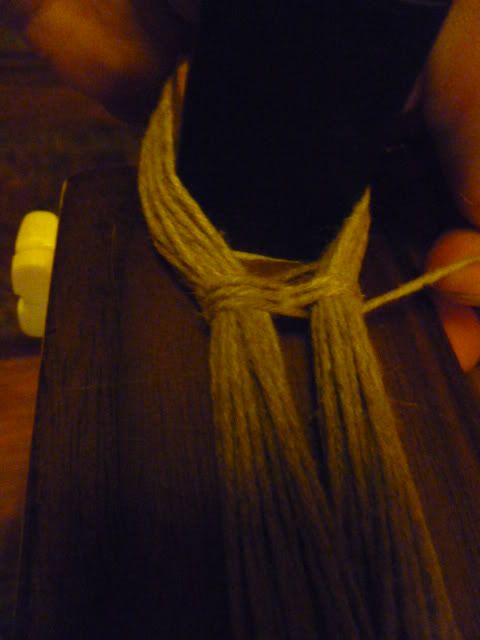


Notice the fid? It is that little gold looking thingie.

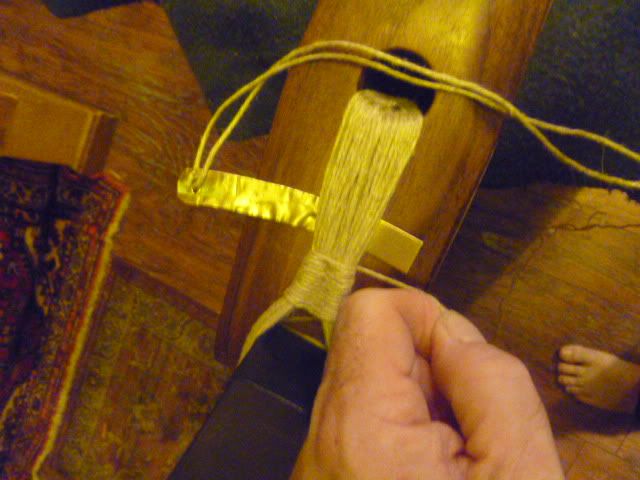
I am not sure if that is even the correct term, but that is what I am calling it, and allows me to pull the thread through the bundles and behind them, too. Mine is made of gold! Yes, pirate gold! Aztec pirate gold! Cursed, too. Or, maybe it is made of brass. I recommend something less able t scratch your tiller surfaces though, and will have to make a bone one later. For this time, I used this, and the minute scratches I foolishly caused I can buff out and make go away, mostly. Chalk it up to bad craftsmanship in this instance.


So, 13 revolutions had the two sides of the binding skein close to each other, which I hope the photos show.
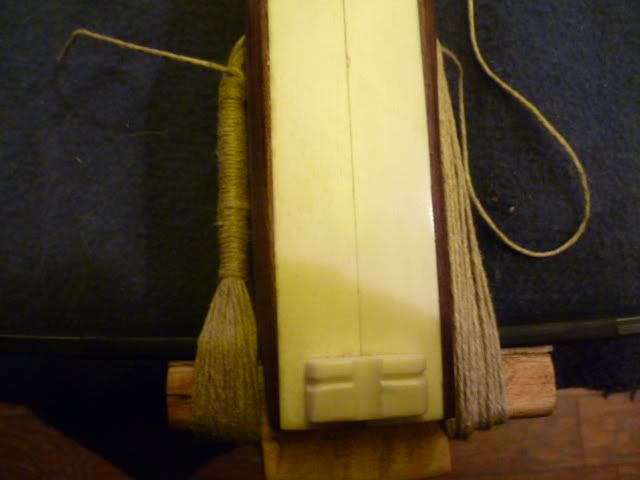
This shot shows both sides from above, with one side all bound and the other still pissed it will loose its freedome
Then, I began the second set of wraps, this time behind the skein bundle and around, and around, and around.

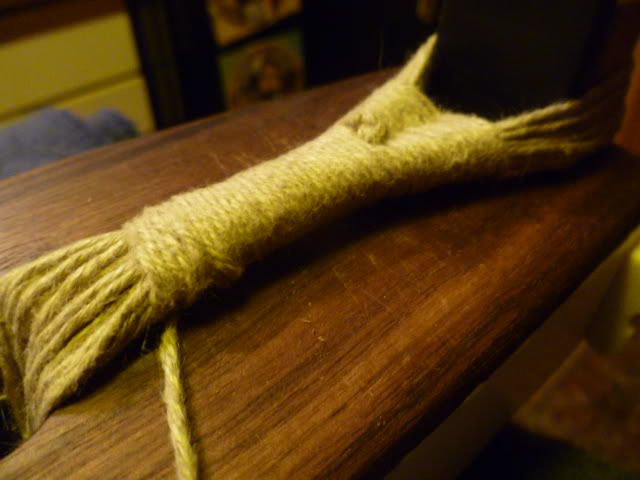
Keep going, making sure you lay the thread on carefully so each adjacent threads shows no gaps, it lays nice and neat, and is happy. Constantly be vigilant for knots forming (you can see that was an issue on the second side, but it doesn’t look too, too horrible, and to abort now and start over for one little knot would have been madness).
About maybe 20 wraps moving aft, it starts to get super tight, and you and the fid will work extra hard. Keep going, stop frequently for breaks and coffee, and keep at it. When you just can’t seem to get the fid in there and are very close to the binding hole, you are about done. I made a half knot, and cut off the thread.

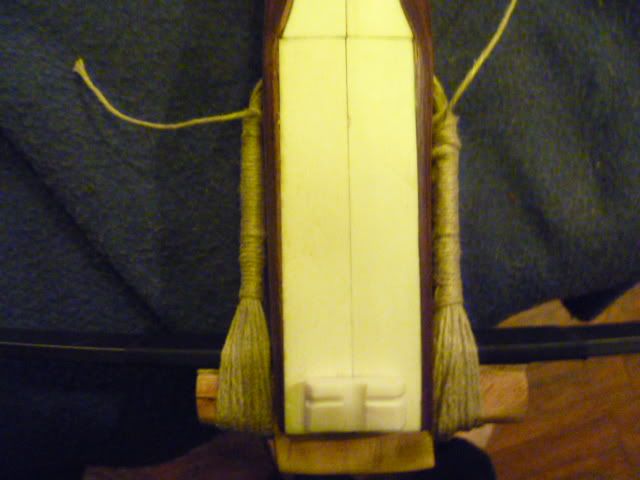

Later, I will probably brush some rabbit or other type of hide glue to help lock in the bindings, but that is probably not essential, and that step could be skipped.
You can see that the second side is not as handsome as the first side. I had a bit of trouble that I didn’t notice, and by then, backing out was going to be really hard, so I kept going on the second stage spiral wrapping. And, there was that little knot, which you can see at what I will call the prod eyelet. But it doesn’t look too bad, and is hard as a rock. The prod is unmoving and that is exactly what needs to happen.
An issue that may come up later is loosening of the prod bindings. It does happen, and generally during wetter, warmer months rather than colder, dryer months such as right now. Sometimes you need to just rebind the entire weapon, but that is a case by case basis, and nothing to worry about right now.
And there you have it. Next up is weaving on the stirrup. Stay tuned.