As you can see I put my wool about 3 inches thick.
then you can start painting the wool with the satanite,you should paint it to bout 1/8 thick the let it dry then do it again till you have bout 1/4'' thick satanite on the walls.( did not snap a picture of this step , sorry)
Then you have to make your door. I used the end of the compressor tank and welded a door hinge and handle on it.
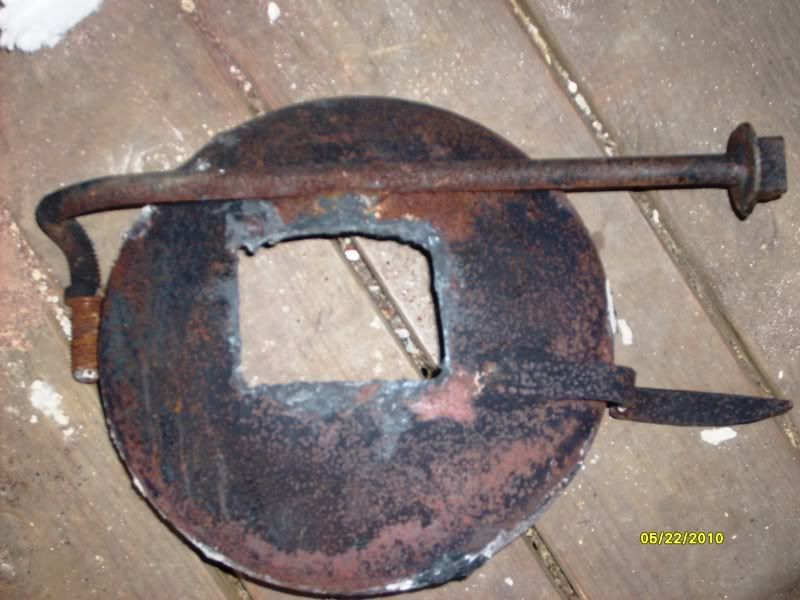
Now flip it over and coat the inside of it with the satanite to give the wool something to hold on to.
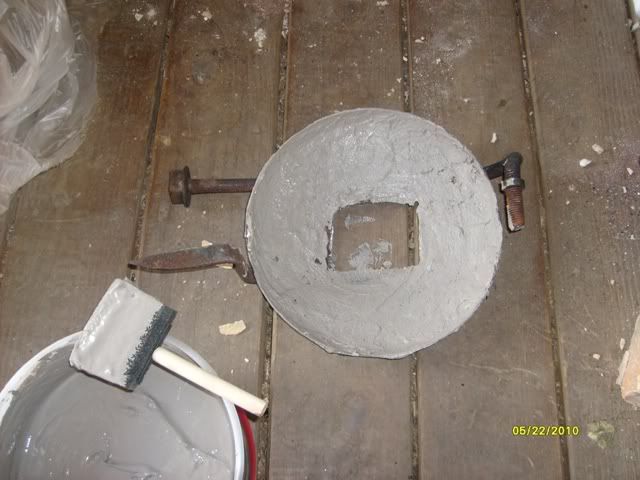
then lay your wool on it while the satanite is still wet, let it dry then coat it as you did the forge.
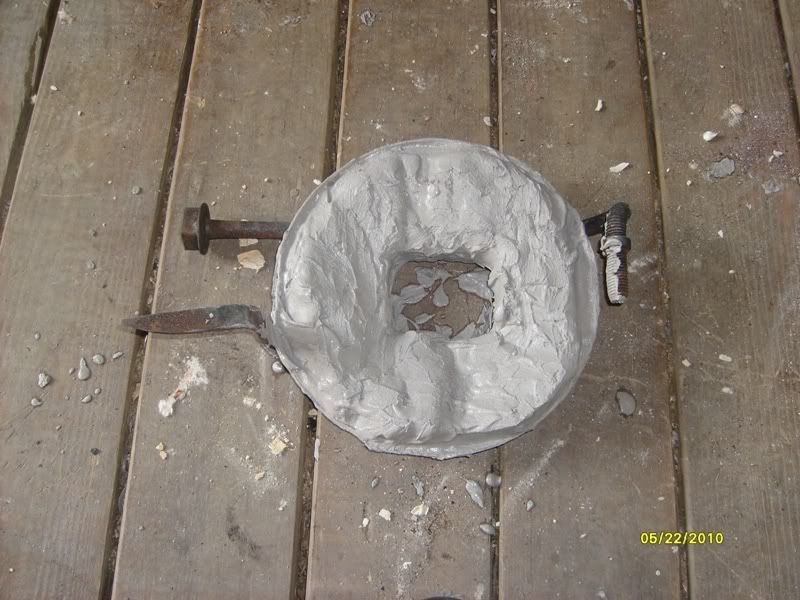
Now i forgot a step in the above post. you need to weld a burner tube to the side of the forge, so your burner can slide down into the forge. As you can see , I used run of the mill pipe fitting. one reducer and a piece of black pipe, you should do this at the start of the build. lol i am BassAkwardIt should be welded on the side at an angle as to creat with the fire a vortex that spirals around the inside of the forge..
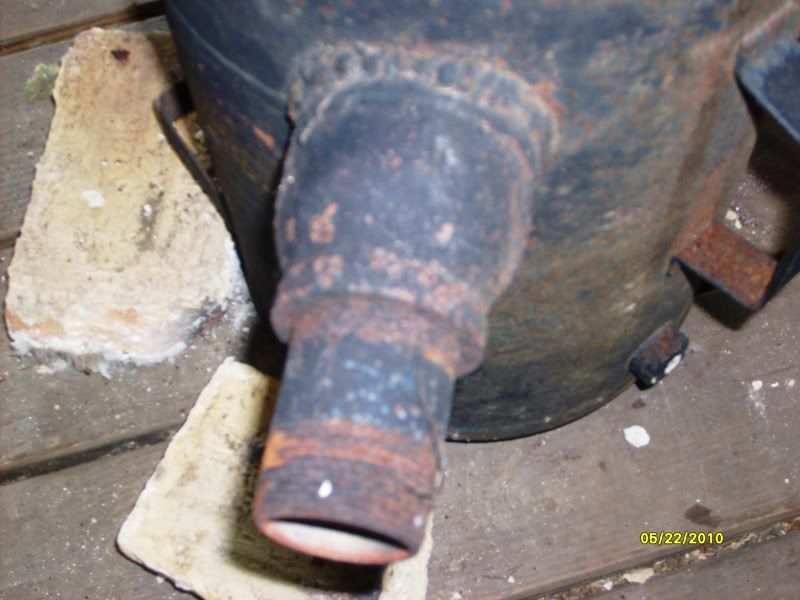
That should take care of theforge body, tomorrow evening I will take detailed pictures of the burner, I am useing a blown air burner, so the parts are important to see up close